Securing 45,000 bolts on Botlek Bridge in Rotterdam
The spectacular new Botlek Bridge near Rotterdam has undeniably been one of the biggest challenges of the A15 connection project. No less of a challenge was securing the whopping 45,000 bolted connections within the allotted time. Thanks in part to equipment from RAD Torque Systems, the job could be completed well ahead of the deadline. Hans van Biljouw, Sales Engineer Bolting at Bus Industrial Tools, explains how this was done.
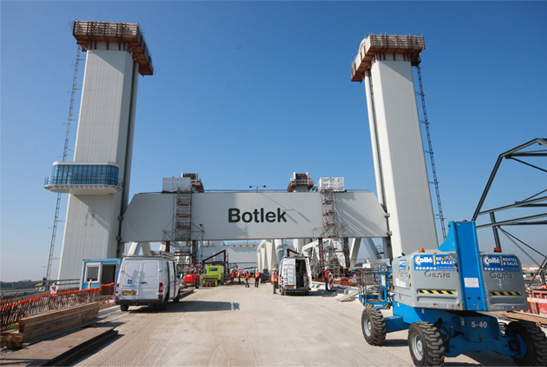
In Rotterdam’s port area, the new Botlek Bridge has been under construction for the past 3 years. With its length of 1,200 meters, lift towers 64 meters high and the 2 bridge decks, each the size of a soccer field, the lift bridge is the heaviest and highest in Europe. The lifting system allows the 5,500-ton bridge decks to rise and fall 31 meters at lightning speed, giving the bridge even the highest elevator frequency and elevator speed in the world. In short, a unique project that is part of the widening of the A15, the lifeline between the Maasvlakte and Rotterdam’s Vaanplein. For the execution signed A-Lanes A15, a construction consortium formed by Ballast Nedam, John Laing, Strabag and Strukton.
Problem with bolted joints
Hans van Biljouw is a specialist at Bus Industrial Tools in everything to do with the controlled hydraulic or electric tightening or loosening of bolted connections. In the past year, he has been closely involved in the construction of the Botlek Bridge.
“A super nice project,” he thinks. Van Biljouw became involved with the Botlek Bridge when he was there to calibrate a hydraulic torque wrench used to tighten some 800 M40/M50 bolts. However, when he saw the low flow rate of the pump, he did foresee some problems. In his opinion, the capacity was insufficient to continuously tighten bolts with, so he recommended not torquing, but tensioning. “This is much faster than hydraulic torquing, more accurate and much safer. It resulted in his employer renting hydraulic equipment suitable for this purpose.”
Faster with RAD
Another request a few weeks later; this time to help assemble the bridge guiding boxes. These “guiding boxes,” essential in raising and lowering the bridge sections, were secured using hydraulic torque tools. They are large plates that had to be torqued with 36 M30 bolts each and then torqued another 90o. But the crew working on it didn’t get it right. “With all due respect to the men who were working there, they used the wrong methodology which created uneven tension in the bolts,” Van Biljouw said.
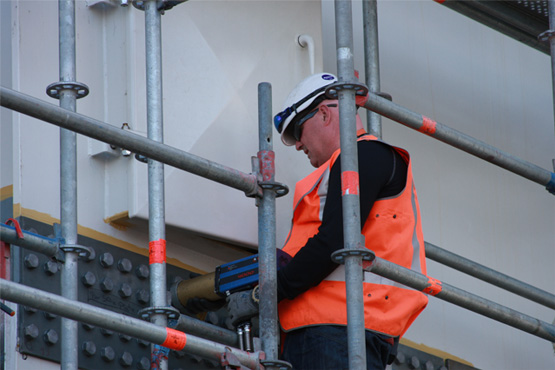
Speed, by the way, was also a requirement. A deadline of 24 hours had been set for each bridge deck due to ferrying to the piers. However, the first deck still took 28 hours due to various imperfections and missing parts. The second deck, for which 17 hours were available, they did in just 12 hours. “This could never have been done with hydraulic torque wrenches,” says Van Biljouw, “we would have been at least 12 hours longer. In fact, with hydraulics it took 2.5 minutes per bolt; with the RAD wrenches we did it in 40 seconds.”
Digital setting and recording
A huge plus of the electronic E-RAD key used at the Botlek Bridge, van Biljouw also finds that parameters such as tightening torque and angular rotation can be set digitally in advance on a touch screen. This makes the system user-friendly, prevents operating errors and guarantees high accuracy. In addition, all forces and stresses in the bolts are digitally recorded and stored; fully in accordance with the client’s requirement.
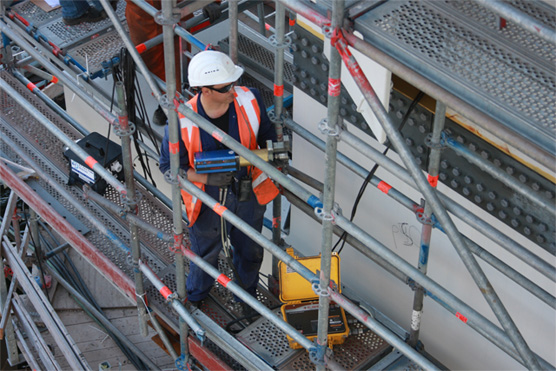
The only limitations of the RAD Torque wrenches, Van Biljouw discovered, are the requirement that there be sufficient space to place the pistol-shaped machine and the maximum torque of 10,000 Nm. More would require hydraulic tools. So in the end, a mix of electric and hydraulic tools was used. “But most of the work we did with RAD,” he says.
A total of some 45,000 bolted connections were tightened at the entire bridge. That meant first torquing and thus preloading, waiting for several hours according to regulation, and then torquing again at 90o angular rotation to achieve the correct prescribed torque. “So we dealt with, say, every bolt twice and of those, only 15 broke.” According to Van Biljouw, it says a lot about how well RAD wrenches work.